|
From the Boatshop
by Ron Magen
"That FREE Lunch I mentioned . .
."
A few months ago I was fortunate enough to be one of a small number of
people from across the country selected to do some ‘real life’ testing of
a special type of table saw blade. Anyone who also ‘follows’ the
rec.woodworking newsgroup has seen the frequent threads of Blade vs Blade.
It’s like the MAD Magazine ‘Spy vs Spy’ segment. The usual propagandists
are the Forrest vs the Freud line of blades. Both are high quality with
Carbide-tipped teeth. It has been amusing, to me, reading how heated these
discussions become. Why? - because in almost the same sentence as the
justification that ‘their’ blade cuts to a 0.000 degree of accuracy -
‘they’ talk about allowing for continual ‘wood movement’, or expansion &
contraction, due to the normal changes in the environment & seasons!!
Also, any boatbuilder KNOWS that NOTHING of wood is ever built ‘exactly to
the plan’. There will ALWAYS be some little ‘hitch’ or adjustment
necessary to get a ‘fair’ curve to a sheer or chine. That’s why the ‘Art’
of Lofting. It is also the nature, and joy, of working with wood.
What makes this blade ‘special’ it the material on the teeth. Instead
of Carbide it is a CERAMIC. Before I even put my name into contention,
there was a lot of heated messages about this being a scam, etc. In my
past I gained an Associates degree in Mechanical Engineering. The ‘Lab’
was a very large and varied machine shop. All the equipment was
‘experienced’ . . . donated by numerous local manufacturing concerns. One
of the things we had to do was grind our own toolbits for the metal lathe
work. We started with ‘tool steel’ blanks just like the ‘real’ machinists.
Later, with the much greater use of automation and high speed production,
the ‘bit holders’ used pre-formed replaceable ceramic inserts. Therefore I
knew the material & concept was correct.
I received notification that my name had been selected, and would I
call a certain person at the company that was manufacturing the blade; the
testing was being arranged by the company that produced the Ceramic
Inserts for the blades. I called the toll-free number and discussed MY
specific requirements. For ME there is no ‘long runs’ of any
one-type of cutting. In one day I can be cutting sheet goods, ripping a
1/16th off a Mahogany plank for a precise fit, cross-cutting pieces of Oak
or another hardwood for frames or a stem, then cutting 2x6 Pressure
Treated planks for keel supports, or maybe ‘nibbling out’ a wide dado or
half-lap in Cedar for a Rose Arbor for Joanne. All with ONE BLADE.
What I NEEDED, and I suspect it is the same for any number of you, was
a "Jack-of-all-Trades". Would it be a compromise? . . . OF COURSE. Would
it be better than a ‘standard’ 36-tooth Carbide Combo blade that was on
the saw now and that had done all these things admirably ? THAT was what
they wanted to know. What I WANTED was a blade that would give me an
accurate and clean cut in plywood sheet goods . . . the ubiquitous
building material of TODAY. It is also one of the top materials when it
comes to dulling blades; the blade has to rip & cross-cut simultaneously
through layers of wood & glue lines. I also wanted a clean exact rip cut
to trim that last 1/32 for a friction fit, then cross-cut that same piece
of Mahogany (another naturally abrasive wood) for a tight corner. Don’t
forget that I wanted the same clean cut in the softer Cedar which has a
tendency to leave a ‘frayed edge’ when cut. There was also the clean angle
cuts on the Pressure Treated ‘2x’ stock - I make my own tool stands & saw
horses.
What we decided on was a 48-tooth, ATB grind, 10-inch, CERMET blade.
This would give me a finer cut than a 36-tooth Combo blade, a good ‘glue
line’ rip cut, and a clean shearing cross-cut.
Reading the accompanying literature, and ‘listening’ to the
rec.woodworking newsgroup, it seems these types of blade tips are not new;
they have been used in the commercial wood product manufacturing industry
for several years. However, Tom Walz’s company {Carbide Processors, Inc.,
of Tacoma, WA} has developed a ". . .superior tip and brazing technology".
Their claim is that "(all) Ceramic Tipped Saw blades cut cleaner, faster,
longer and quieter with less effort". From what I can gather, this series
of ‘real life’ tests (as opposed to the in-depth commercial
test-to-destruction already concluded) is focused on extending the market
to, ". . . skilled artists and serious amateurs"
While I have no measurable way to test the actual DbA {sound level} of
the blade, and a ‘life test’ as to how often and how many sharpening’s
would take more than a year, I can attest to the apparent cleanness of cut
and the ‘intangibles’ of how materials feel when being cut.
In the most simplistic sense . . . it has done everything I have asked
it to. It has cleanly cut everything I have ‘fed’ it, including some
‘freehand’ work on full sheets of ply and some angle cuts. [NOTE: a
REAL NO-NO on a tablesaw, especially with the guard removed !! NOT,
repeat, NOT a recommendation] While I can’t comment on Corian or
Melamine, the most troublesome & abrasive material I use is ‘3/4 inch’ OSB
- clean cuts, no problem.
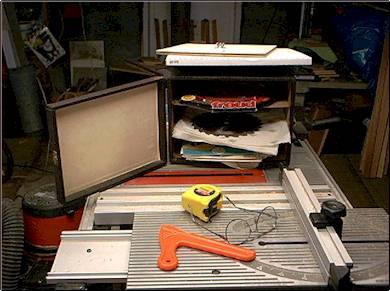
My ‘tablesaw history’ has had five stages, so far. As a teen I used an
‘accessory table’ that held a circular saw upside down. Years later, when
we bought our house, I got a B&D 8 inch ‘benchtop’ {probably made out of
old tin cans} with their punched out steel blades. Then I ‘discovered’
Carbide blades, and figured a way to ‘shoehorn in’ a ‘good’ 9 inch Oldham
blade {couldn’t lower it or raise it all the way without hitting
something, but it worked . . . and I was lucky !!}. Finally I decided to
get a ‘real’ tablesaw, and decided on the 10 inch Ryobi BT3000 with the
Cast Aluminum top. It came with their 36-tooth Carbide ‘combo’ blade. The
first time I used it, it was both a revelation and an epiphany. I
assembled it per the instructions. I checked all the ‘tuning measurements’
with my basic tools (square, tape, etc); nothing exotic like feeler or
dial gauges, or micrometers. Then I grabbed a chunk of that ‘old standard’
- a ‘2x4', Pressure Treated I remember. Raised the blade, under the guard,
aligned the ‘miter slider’ & wood for a 1/4 inch ‘slice’, turned on the
saw and smoothly ran it through. Nothing - no resistance, no vibration, no
sound other than the ‘air noise’ of the blade. O.K. - I’m not used to the
adjustments on the saw. Raised the blade about 5 turns more, and slid the
wood over about 3 inches. Eased the wood through - the same result . . .
almost. This time a piece of the ‘2x’ was left behind !! I simply couldn’t
believe it - it was literally like cutting butter. I called Joanne and had
her run a piece through . . . just to be sure it wasn’t only me. After
getting a bit more familiar with both the saw & 10 inch Carbide blades, I
developed the ‘touch’ for this ‘system’. When I first used this CERMET
blade, it was re-living that moment all over again.
There has been some negative comments about the blades from some
people. Often it turns out to be a person who simply tried it on someone
else’s machine; using their usual cutting technique. The comments
typically center around cleanliness of cut, tooth marks, or burning. I
believe there are a couple of answers to these problems. [NOTE: I’m
speaking from MY point of view and experience, I can’t speak for
the other ‘testers’. 5 got blades by lottery, 2 of us were selected
as ‘Professionals’]
1) Define YOUR requirements -
I knew the particular tasks that are done on a regular basis. There
are simply no long runs of any specific type of cutting task, i.e.
ripping or cross-cutting. The ‘most used & most useful’ blade style
had to be a General Purpose or Combo blade. Agreed, I wanted it
‘skewed’ toward the finer & cleaner cut parameter.
2) Read, TEST, & Learn the idiosyncrasies of YOUR blade -
Each blade, tool, & person is different. Each has it’s own ‘feel’
and range at which they work most efficiently and produce the best
results.
We all do many things unconsciously; like driving or walking. {No
jokes, please, about some people having trouble walking and chewing gum at
the same time}. In the same manner we also get & use ‘cues’ without really
thinking about them. My old 4-banger pick-up is a manual 5-speed, and I
drive ‘by ear’. Using ‘feel’ and sound while feeding a board through the
tablesaw blade, is another example. You just ‘know’ when the engine is
lugging, and when to shift up or down. You just ‘know’ when the motor is
being overloaded, and to ease off on the hand pressure.
Something that seemed naturally intuitive to me, and the entire concept
of ‘power tools’, is to let the tool do the work. The experience of
several well-known woodworkers agrees. In any number of their books, a
‘Troubleshooting Chart’ is usually included.. Where the ‘Problem’ is
listed as "Blade Stalls", "Burn Marks", or "Tooth Marks / Rough Cuts" the
correction is typically - - - "Allow the blade to cut at its own
pace". One of ‘operating hints’ about the CERMET from the company
is to: "Run them hard, move the material through the blade FAST. For me,
this was the most difficult adjustment to my technique. {The effect
seems to be analogous to cutting your lawn with either a bagging mower, or
one that keeps re-cutting the debris into mulch. An example would be the
impacted clippings on the bottom of your mower - they’re surprisingly hot!
} I was getting some burning, especially with some thin trimming cuts. I
was using my usual style, easing the work through, the Shop Vac making
more noise that the saw. For an experiment, I turned off the vac, got a
long piece of 2x ‘scrap’ and started making cuts. Faster and faster feed
cuts. I really had to move fast to hear a change in the tone of the blade,
and NO BURNING.
I’ve now used the blade for a couple of months; it was even exchanged
for another because someone else had a complaint about their blade,
so the company exchanged all the test blades. A real ‘life test’
will take a year or more - - for MY situation. However, for
Tom Walz to wait that long would be unfair. So far it has ripped,
cross-cut, made angled & ‘free-hand’ cuts, and ‘nibbled’ half-lap joints
in 2x6 Pressure Treated material. I can’t say that it, ‘cuts paper like a
Ginsu knife’ simply because I haven’t tried it !! {Hummmm?}. By the
same token, although I have used blades from ‘stamped out’ steel, strange
4 & 6-tooth carbide, ‘Pirana’ blades, and various sized B&D, DeWalt, &
Oldham ones, I only considered my 3 - 10" blades as QUALITY ones. [a Freud
Fine Cross-Cut, Freud Thin-Kerf Rip, {my 15-amp saw is considered
‘underpowered'} and the 36-tooth Ryobi] I have never tried the much-raved
about Forrest Woodworkers, nor Dave Carnell’s Matsushita’s.
Before the testing started, I checked all the alignments, cleaned all
the sawdust and debris from the mechanisms, and lubricated the appropriate
points. Nothing looked other than dusty after two + years of use.
‘Underpowered’ or not, my saw and the CERMET blade hasn’t had any problems
doing anything I have asked it to. I’m still learning; every time I try an
operation I haven’t done before there is a learning curve. I also tend to
make jigs & templates for almost anything I think I’ll make more that one
of. The blade cleanly cuts multi-ply ‘Baltic birch’ and 1/8 inch Tileboard
with equal ease.
Before I changed out the Ryobi combo blade I made a few ‘test cuts’ and
put them aside. [I had the blade professionally inspected . . . it was
only about 10% off from the ‘sharpness’ of a new blade; not numerically
significant in a test of this sort] The CERMET blade cuts were
slightly cleaner & smoother.
From their website {www.carbideprocessors.com},
the cost of the CERMET blades is not cheap. In my case, although the 10
inch CERMET blade is $88.oo more, Forrest does not even have a 48 tooth
‘All Purpose’ blade. Additionally, the website recommends using a blade
with 2/3rds as many teeth as the equivalent carbide blade; therefore my
ceramic teeth gives a cut equal to 72 carbide teeth. The cost of having a
Carbide blade sharpened locally {suburban Philadelphia, PA} or sending a
CERMET back to Universal Saw Company was about the same. HOWEVER, if the
‘life per sharpening’ is even on the low side of what’s claimed, {"Stays
sharp 5 to 10 times as long {as Carbide}"}, than the total ‘cost to use’
would be at least 80% LESS than Carbide tipped. If the numbers hold true,
the CERMET comes out ahead.
Should YOU buy this blade? I can’t say that my results
came from technique, or the specific saw. From all the discussions,
comments, and adverts about ‘Super Quality’ blades, a lot of people have
them and have spent $130 and up per blade. If you have the ‘Basic 3'
blades for your 10 inch tablesaw {NOT counting that Chop or Miter Saw}
that’s a LOT of money. That total is the cost of my saw. Of
course, if you have a $1200.oo + Cabinet Saw it’s another story. IF
I had just bought a saw, had NO blades, YES, I
would buy this blade {and this configuration} as my ‘basic,
do everything good’ choice. As I grew in skill, or specific type of work,
I would then buy blades specific to the job. By the same token, If I was
advanced and 90% engaged in specific tasks, I would get a CERMET
blade designed for that task. If I could afford it, I would get
another CERMET designed for ‘general purpose work’. If not, then a less
expensive Carbide one.
While I haven’t seen any advertising in the usual periodicals, the
blade lives up to the claims on the brochures included with it. Your
money, your choice . . . I’ve made mine !! |