Guest Column |
|
By Roy McBride - Cape Town, South Africa
ckdboats.com
Do Yachts Need to be so Expensive? |
 |
A decade back, Neil Rusch, the then editor to 'SA Yachting’, a long running South African sailing magazine, asked if I would draft a story on how I thought yachts became the expensive things they tend to be. The story was written and duly published and I would like to think it might have given a bit of 'food for thought' to any one who may have had the time to read it. It was titled ' Yachts Are Not Expensive, We Make Them So'
So now ten years on, we are near the end of the year 2005, I think its time to rewrite that story... with a possible rethink on some methods and systems we can now look at to save both money and labour, as well. The basis of the idea is to show, in fact prove that with some thought and possibly using your own hands (by building one of our kits but certainly not restricted to that), anyone who wants a yacht can have one. The truth is keeping things simple and if you have a small cash book you will probably end up with a small boat but that is no hardship, as long as you are sailing.
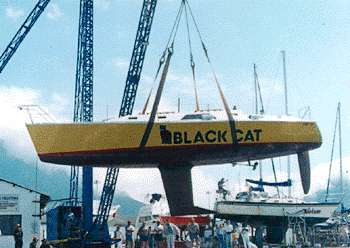
What makes a yacht?
That’s a question that probably has no easy answer, however, the classic converted fishing craft of the late 1850s to mid 1900s made their presence felt as yachts. Those boats were re-fashioned as day or weekend over nighters and fitted out with luxury accommodation. That’s a start line, pity they then would have sailed that much slower due to all the extra fittings installed. As time passed those fishing craft, driven only by sail gave way to sail and power, then just by power. As they got older and became derelict, they finally rotted away; some new source of yacht was needed. So, probably the same yards that had built the sailing fishing craft were sought out to build purpose hand built yachts... an evolution of sorts.
Those heavy boats with bulbous bows, slowly changed to become the full deep keel and graceful overhangs we see on boats from the early 1900's. Many of the new style boats just had a basic sail plan, gaff rigged and low cost and a hand painted interior. Find one of those and you will find a boat that is functional without any fancy parts. It's all hardwood dead eyes in the rigging and galvanised cast Iron deck fittings, then comes 'The Bronze Age' in boats and with it the added costs. Bronze against Cast Iron; from then on we are sort of hooked into a spiral of extra costs... you can add in an engine at this time too.
How to save money by building your own boat?
Here is a case study that proves its possible, even more so, if you go the kit boat route, which was not even thought of when the boat in question was built. The boat that follows can now be supplied as a complete kit, that’s bulkheads, Hull & Deck panels, Cockpit & Coach roof. Now, all the builder has to do, is the assembly, in truth this is not really boat-building, just boat assembly. The end result is the same; you end up with a sailing boat and at a much lower buy in price than buying a hull & deck unit from a boat yard.
Back ten years ago, at the time I was drafting my story, yacht designer Dudley Dix was about to turn over his new yacht. A Plywood/Epoxy 'DiDi 38' and eventually it was named 'Black Cat'. Then a Peanut Butter manufacturer of the same name, became a major sponsor, that boat was a groundbreaker in that the design was done to suit Dudley’s own cashbook and a change in wood/ply/epoxy construction. In that it was the first such Radius Chine design by Dudley, possibly by anyone. I became one of the crew that helped turn Dudley’s new hull over; it was a day to remember and a good after party too...
turning the hull - Dudley’s back yard, Hout Bay |
When the hull was the right way up it was easy to see what made such a boat, materials wise. Not a lot really, being all Ockume Marine grade ply's, Mexican Red Cedar Stringers and Epoxies to glue it all together, it was as minimal a cost structure than you can find. Even more so today, if one is considering a GRP hull and deck purchase. As Oil prices Surge to U$60 a barrel and beyond, we will soon see construction of yachts in GRP spiral as the Polyesters used in construction rise with the oil price. We are talking double the cost here too, ok, the Epoxies will follow with an increase in price but our Plywood/Wood/Epoxy kits only have around 15% as the Epoxy component, so the extra cost rise, percentage wise, will be very much less that the GRP boats...
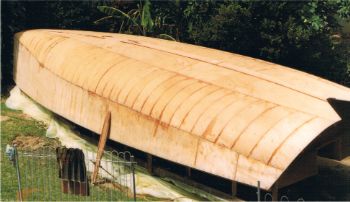
When comparing Plywood/Epoxy to GRP construction we will see a saving of a different sort here too! Weight, a Cubic Foot of Marine Plywood is said to weigh just 44 lbs. while a Cubic Foot of GRP laminates some 100 lbs. While I have never actually weighed the two, it does make some sense...of course weight costs more money in this case, a good reason when a lower price is a factor and a fair reason to consider plywood/epoxy Boat.
After Dudley got his hull turned over, he then fitted the deck and prepared the boat to race in the 1996 Cape to Rio yacht race. He did the race twice in the same yacht, plus one return leg too... sure proof that his design and construction methods really do work... I think its correct to say that Dudley had a seriously tight cash book right then. His other boat had been stripped of all its gear and where possible, those parts recycled and installed into the new boat... the old hull was then sold on to a new owner and most probably assisted with the purchase of a brand new Diesel Engine.
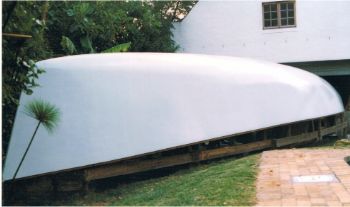
The boat was fitted with a new mast and new sails. That was nearly as far as the new parts went. The interior of the boat was left as what may be termed 'Spartan'. This was a Race Boat after all and just like those converted Fishing Boats back in the last century or so, interiors add weight! So, Dudley’s boat was just painted, with very little trim... actually none, as the writer was commissioned to add in trims and a Teak and Holly Floor, for a new owner a few years later... at not a little extra cost, both in weight and money of course...
Dudley Dix comments:
I sailed her on the 1996 and 2000 Cape to Rio Races. In the 96 race our top speed was 18knots,in the 2000 race we topped 22 knots. In both races we took approximately 21 days to Rio. Despite the fact that the 96 race was a Spinnaker reach/run for about 16 of the 21 days and the 2000 race was a fetch for most of the race, with our spinnaker set for less than five days total time. Our best days run was 250 miles, or on average 10.4 knots. Our average speed across the Atlantic was over 7 knots.
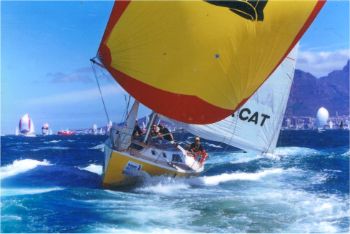
She took 3000 hours of labour; most of it by me working single-handed.
That is quite a boat and its using the 'Build For Less' theory...
So what is this all saying to us?
Less is best sometimes for sure but the problem comes from what we tend to perceive as a Yacht. Go on take out your copy of 'Sailing' or maybe 'Cruising World' magazine, find a nice glossy picture of an advert for a yacht, Mono hull or Multihull. And it will make little difference if its made in China, South Africa, USA, France even the UK, just look at those fabulous interiors! Most are probably better fitted out than our own homes. And at what cost we may wonder?
This is what costs the money! On a Dix 43 wood/epoxy construction, the hull of which took one man just six weeks to build on his own but then two years to fit out to this standard. It was that owner’s choice but a simple off white paint job would have been very much the faster build.
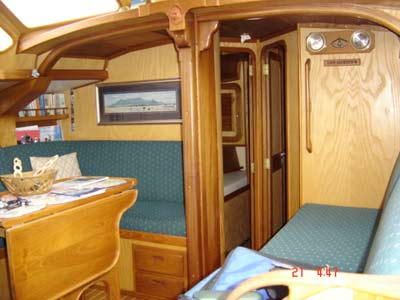
The interior of a Dix 43 - it took one man two years on his own to fit this out, but the same man built the hull in six weeks - also on his own. This yacht could have been sailing years earlier if the boat had just been painted inside with some simple trims but we get hung up with all those pictures in glossy magazines!
You can see where this is going? That’s where the costs are, it’s not the boat around the interior but the interior inside the boat itself that costs all the money!
Also, when I drafted my first story a decade back, I took 'Black Cat's deck plan to three Marine Chandlers and asked for a costing sheet to fit out the boat based on a simple type of deck gear and the like. What I received back from them was an eye opener to say the least. Offers of Self Tailing Winches, top of the Range Deck Hard Ware and even a hot water calorifier from one Chandler, not one of the three stores even listened to what I had said to them re: keeping things simple and low cost.
So based on that bit of simple research, I can only assume that when Mr and Mrs Joe Soap goes into a Marine Supply Store to cost out their intended 'Wannabe 36ft' or other design, they are given prices for the most expensive gear first, that may kill the boats build right there and then, of course. It was that factor that made me realise we make boats expensive but we do not have to.
So use the K.I.S.S factor, or as we all know means 'keep it simple stupid’! The fancy stuff can come later, when you’re best able to afford it, if at all of course.
Moving forward those ten years, can we buy better gear and still save?
Yes, as ever there are a few purchases of more fancy gear that either cost no more or even save you money and extra labour as well. You as the buyer or builder really need to shop around and weigh up what’s on offer from the many suppliers worldwide. For instance you can buy 316 stainless parts from the Far East at a fraction of the cost from Europe. However, there is a penalty to pay, the parts from the far east probably look the same but will not have the same breaking strain when under a full load. So, if your looking at a Race Boat you will need to buy the best but if your just knocking about in a creek or just basic light air sailing, the less expensive offer will do the job.
Sometimes buying more technical gear does make a lot of sense though and at very little extra cost, if any at all. For instance, when the Dix Design Trailer Sailor GRP yacht ‘Zest’, a 'Cape Cutter 19', was launched I asked the builder why he had chosen what looked like expensive Roller Furler Units on the two Head sails. He replied that the items as chosen and made in Australia, actually cost about the same, as would have bronze piston hanks from Sweden! Plus they saved both labour when sailing and space to store the headsails down below when not sailing. That made a lot of sense to me at the time and when carried over to a much larger sailboat, the same is still true! Yes, you spend on the Furler Gear but your sail maker then makes you a single Headsail that covers a wide range of sails. This saved the purchase of at least two extra headsails to cover the wide range of sails normally required; you will need that Storm Jib anyway.
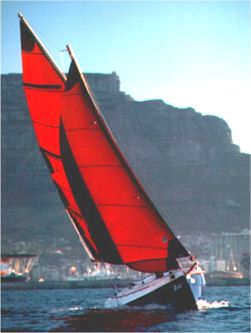
Cape Cutter 19, Zest, hull number one, sailing in
Table Bay, Cape Town, South Africa
There are other areas where spending more to begin with really does make sense. Paints and Varnish are included here. Using common off the shelf Single Packs from your local paint store will be very cost effective, well, to start with at least, they will probably be Oil Based and Thinned with Turpentine. They will look good when applied but only for while. Given a year down in Cape Town, South Africa, the UV (ultra violet) rays will do their damage rather quickly. Using Marine type paints based on P/U (polyurethane) type twin pack paint will last much longer and while you will spend more on the P/U Coatings to start with you will save on the labour by the second year at least. We have a Dix Design 43 ft Ply/Epoxy sailing yacht, its spray painted with a Marine Grade P/U system paint and its been out in the elements some eight years now, with very little degrading that matters. Even stepping on the deck in the same spot each evening for five years shows no damage to the non-slip paints, nothing.
The boats varnish to the Teak Cap Rails and Grab Rails has seen various varnish systems used. Until recently, all Single packs like traditional clear marine varnish and wood coatings with UV stabilisers in them...the traditional type used first was breaking down in just six months. The UV stabilised type around twelve months...
we have been in the water six years come next January, so that’s quite a lot of down time to re coat each year...
So, these past few weeks or so, I've looked at what’s on offer with marine grade P/U clear grade twin packs. (If you need trade names, please email me). Looking at one manufactures varnish handbook, I noted that their top of the range clear twin pack will give six years maintenance free service in the UK where it is made... so for our hard UV we have here in South Africa we can say three years use. Yes the product is comparatively expensive at R265 per 750 ml (one pint?) or about U$42... but look at these numbers that need to be added in each year.
Based on a three year cycle:
- Oil Based Varnish.... R120.1 ltr... labour to sand down each year (I apply all varnish myself) R 500 x 3 years = R1860 or some
US$295 total
- Polyurethane two pack Varnish R265.750ml..... Labour to sand down one year " " " " R500 x 1 year = R765 or some
US$121 total
So there is just no contest when the use of the better product is done, plus in this case the natural Teak Wood Grain shows right through and it took just one 750ml tin to apply a full six coats as well. This means it's quite cost effective really... and as long as I keep the new varnish in good condition, we will just require a light sanding and the application of two more coats every three to four years or so.
Also clever designers are sometimes involved in the evolution of their boats design, often seen as a MK2 version etc, being how to save the cost and the added weight of expensive fittings, which is really what makes the boats expensive in the first place. You can and indeed, should do your own costing here! Take a hull and deck unit, either GRP, Steel, Alloy or Plywood/Epoxy. Each will have its own reason why it's the material for you but they will all cost a lot less than the total of the boats value. Just the hull is said to be just some 15% more or less of the finished boat... so its what we do to that hull unit that costs so much.
This is one area that a designer and a builder can save money for the buyer...as follows,
Take Peter Ibolds classic design the 'Endurance 37', first moulded in England by Tyler’s around 1978. Then in South Africa not so long after, this was a really successful design, much sought after at the time. Now also... but the design soon dated, with its classic long overhangs and full keel, it was good off the wind, good up wind in flat seas but less so in big ones. Having crossed the South Atlantic, Rio to Cape Town and Cape Town to Salvador, Bahia, Brazil, twice in two of these yachts, I can confirm the boats performance good or bad.
They were expensive boats to rig too. Peter Ibold had a good idea with his original Cockpit layout. The Genoa sheets had just one 46:1 Self-Tailer winch, mounted behind the Helmsman, with a line Jammer each side. A neat idea I've seen only a few times since, yes, we are using an expensive Self Tailer winch here, but as you would normally see at least two normal 46:1 winches mounted either side of the cockpit. While in this case the self tailer upgrade is costing no more in this layout. However, you do get the upgrade of the self tailer, a nice thing to have.
Later Peter Ibold redesigned the 'Endurance 37’ (now called the 37 plus I seem to remember). And when I say a 'redesign' I really mean it! This was a clever move, in many ways, both in styling and saving costs. Take a quick look and you saw the same boat but a second look and things were a lot different. On deck the inner forestay and its related deck gear and tracks were gone, so was the bowsprit. I assume the head sail was then smaller and the main made larger, so an easier boat to sail... of course with no inner forestay now a saving was made on not having the Staysail and related standing rigging and cockpit winches to buy either. The boat also had fewer deck hatches, all saving both weight, labour and related costs to both buy and install them...
From the water line down, this was a different boat indeed; the full keel was gone. We now find a large fin keel and a rudder aft with the now normal split in between, the boat would then be more responsive, and it would even go astern where you wanted it. Plus the waterline was longer with far less overhangs each end, all of the redesign shaved off a ton in weight too. So less is more in this case.
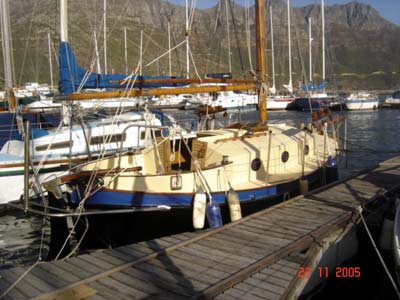
Converted Life Boat - Sailed to Brasil and back on a build budget of U$1270 - which to me proves anyone can be sailing if they really want to.
To end, I must mention a chap I know who built his own steel Roberts Spray yacht. It's about 35ft long, sturdy and Gaff Rigged, he built it all himself too... well he had some bothers with his family, so while they sorted things out (and they did) he built himself a really cute 20ft sailing boat. He used a discarded GRP double-ended lifeboat as the hull. As you may imagine the guy’s funds were all in the larger boat, so he had little to spend, all up and ready to sail to Brazil he spent just R8000, that's around US$1270! This little gem has now crossed the South Atlantic twice, doing daily runs of 120 miles some days too. As it looks now its been repainted and has new spars and sails but it still very much the boat it was. His tiny boat now has new owners and the Spray is now being prepared for a voyage... a happy ending.
So who says boats are expensive now, yes we make them so.
Roy Mc Bride - Founder - www.ckdboats.com
email - kits@ckdboats.com
Cape Town
South Africa
|