Kestrel: A 21' Aluminum Ketch
|
|
by David Godsey - Nehalem, Oregon - USA |
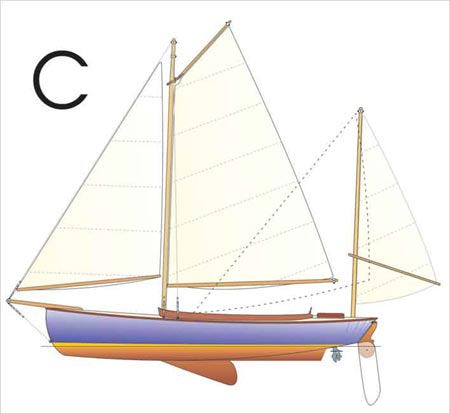
LOA |
- |
24' 3-1/2" |
LOD |
- |
21' 8" |
LWL |
- |
18' 9" |
Beam |
- |
6' 1-1/2" |
Draft |
- |
8" up/5' full down |
Displacement |
- |
2,110 lbs. |
Hull Speed |
- |
5.83 kts. |
Having been occasional crew on an old 20' Pearson sloop over the past two summers, our family has been re-bitten by the sailing bug. The Pearson can only go out at significant high tides and is prone to spinning to leeward when her heavy center board gets mired in the mud. It is no wonder that she is the only sloop on any of our coastal bays. With a suitable shallow draft boat, we would have near total ownership to all our Tillamook County waterways. There is lots of the famous cheese, mucho cows, commercial and sport fishers, but no sailboats except for the occasional blue water sloop going straight from moorage to the Pacific.
Over time, aluminum emerged as a possible approach but we had never heard of an aluminum sailboat except for an infrequent appearance in on-line used boats listings. Aluminum cuts and forms like plywood, never dry rots and would hopefully reduce construction time. Leaving her outside during construction wouldn't be a big deal, either. My son works part-time for a custom aluminum boat builder so the welding issue was solved. The painful cost of marine plywood has reduced the differential between a wood/glass sandwich and metal – another justification. Most hard chine designs looked adaptable so several months were spent absorbing books and surfing the internet for inspiration.
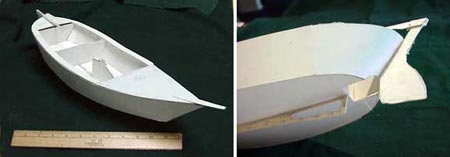
A pre-Riccelli cardboard model by the author
Our design objectives were (1) an easy-to-fabricate shape with (2) a hidden motor well, (3) a flexible sail plan for our unpredictable coastal conditions and (4) be able to scoot across those shallow Oregon tidal flats. Several sheets of mat board and dozens of hot glue sticks later, I had a model that looked pretty boat-like. Her rounded stern gives it a classic look with lots of space for the motor, fuel and aft storage. Slicing up a pricey chunk of metal for a hull designed by this clueless beginner didn’t seem smart so some help was in order. Paul Riccelli, a designer in Florida, provided excellent design concepts backed by a solid grasp of sail physics, common sense and personal experience.
click image above for larger view
After many emails, several iterations, even more models and extensive conversations about sail plans, the result is the Kestrel. She borrows elements from the Stevenson Weekender and other similar hard chine hulls but drafts much less. The sides are to be cut from a single sheet of 0.125 (1/8”), six foot by twenty foot plate. The stern plate will be lightly rolled and lap spliced one per side. The bilge plate will be spliced from smaller, less expensive sheet stock and scrap. Our next step is to build a full-size, half-hull to generate door skin cutting templates. Once the metal is cut with a circular and saber saw, the pieces can be hauled to the welder and tack assembled in a few hours.
The first version, pictured above, is open hull with lots of deck for coolers and big Chinook salmon.
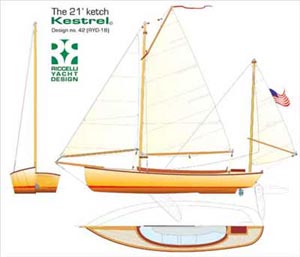
click image above for larger view
Paul has just finished a redo on the hull including altering the rudder arrangement and a few other details plus better line weights (see above).
You can reach the designer at:
Paul Riccelli
34539 Marshall Road
Eustis, FL 32736
352/357-1248
gailc75@juno.com
|