After having two kayaks and one canoe under my belt, I felt it
was time for a change. Looking at my options, and given my limitations
with tow vehicle and garage space for building, I saw two possibilities:
a small sail boat or a small motorboat. Although a sailboat seemed
like a great idea, I had to look at the primary reason for making
another boat, besides having something to do of course. Since
my wife and I love to fish down at the coast, and the wind is
a constant companion, we are limited to how far we can paddle
out to get to the fish. It would really be nice to be able to
get out further in the bays and explore all of the shallow lakes
and other fishing spots that are currently out of reach.
Although I started out in a sea kayak, which is great for paddling,
it really isn't the best thing for fishing, especially with the
muddy bottoms that one encounters around Port Aransas and the
Light House Trails area. That led to canoe, which is great for
fishing, but quite susceptible to cross winds. And in the spring
time, when the winds howl at what seems to be hurricane speeds,
it severely limits our nautical range. We still use the canoe
frequently on lakes and rivers, but for the coast, something else
was in order. Enter the search for a small motor boat.
My requirements were as follows: 1) Either lapstrake or glued
lap strake design. 2) Ability to handle up to a 10 hp motor. 3)
Light enough to be towed by my vehicle (4-banger truck) 4) Flat
bottom for fishing the shallows of the Texas coast (although I
really like the way a V-bottom looks, it just isn't practical
for my intended use) 5) Plain old good looks. I spent a few weeks
looking at various designs, and finally decided on David Nichol's
Lutra Laker. It satisfies my requirements
and has a few bonus features, the most notable one being a raised
platform on the front to fish from. The other feature being several
water tight storage areas at the bow, stern, and amidships.
Although I don't plan on stuffing sleeping bags and gear in these
compartments for overnight camping trips or the like, I like the
safety floatation aspect that these offer. I never realized how
important this quality is until the first day I took my canoe
out and intentionally dumped it (near the shore of course). Long
story short, if I would have tried to flip it back over from the
turtle configuration, it would have sunk. That little sea trial
really opened my eyes and brought safety back to the forefront
of my thinking. Keep in mind, we always wear our PDFs when out
in the kayaks or canoes, but to know that the canoe, once flipped
has to be towed back to shore upside down before we could upright
it was disturbing to me. There are those out there who may be
able to flip it back over in deep water, but I ain't one of them.
Anyhow.. I digress... back to the Laker.. I wanted to talk to
David about whether a feller like me could put one of them there
boats together without any glued lapstrake experience. David assured
me that between the video, plans, online, and phone support, that
I wouldn't have any problem. So I asked my wife if I could have
an advance on my allowance to purchase plans and materials. My
advance was granted and I was off and running!
The plans arrived a few days later with the materials list. I
ordered all the epoxy, glass, and miscellaneous materials on line
and made a quick trip to Houston (I live in San Antonio) to get
the BS 1088 Okoume plywood (the stuff is absolutely beautiful
by the way). The first order of business was lofting, which I
had heard of, but never tried, and I soon found out that the hardest
part of it was switching the brain into the "lofting"
mode of feet, inches, and eighths. I have wondered why this convention
is used instead of what I call plain old measurements, and I'm
sure someone smarter than me, somewhere, came up with it.
Anyway, after one form I was in full lofting mode and quickly
completed all eight forms on 3/4" particle board. The transom
was lofted on to 9mm ply. The sawdust was flying from my circular
saw soon thereafter and before I knew it I had a nice stack of
forms. On to the next step... the strong back. Since I already
had one from the other boats, I just had to reassemble it. That's
when I found out it was a foot and half too short, so I cobbled
an extension together and screwed her on, bringing it to proper
length.
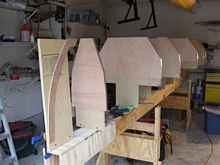 |
Particle board forms |
Then I marked off my form measurements and began assembling all
of the forms on to the strong back. I wanted everything mounted,
and leveled so I could use my eyeball to see if I had made any
errors in the lofting process. It appears I had everything right,
so the next move was to start cutting out the knees and bulkheads.
With height measurements garnered from the plans, I temporarily
nailed the
6 mm ply to the forms and, per the instructions, used a router
with a flush cut bit to cut the forms out. I used a 1 ¼"
hole saw to cut out a "mouse hole" for the water to
drain through.
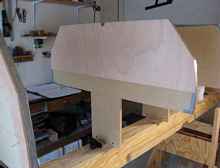 |
Mouse hole |
The next step was lofting the stem on scrap ply to make a template.
Then I temporarily mounted it to do another eyeball measurement.
Things looked good there, so I epoxied two 9mm scrap pieces together
for the final stem. Once dry, I traced the template and cut out
the final product. In addition, per the instructions, I put a
bevel on the sides using my trusty Shintu rasp.
Beveling the stem will allow the planking to lie flush against
it. I also left about a quarter inch flat on the leading edge.
For the final mounting, the temporary vertical mounting form was
cut short of the where the garboard mounts to the stem.
Along side of this process, I was also putting the transom unit
together. Form 8 has two braces mounted via cleats, epoxy fillets,
and tape. These braces are also glued to the transom in the same
manner, and they also set the angle of the transom. The exact
angle escapes me, but as suspected, the transom angles towards
the front of the boat from top to bottom as viewed from the side.
With the transom mounted it is now time to start splicing the
9mm ply together to form the bottom.
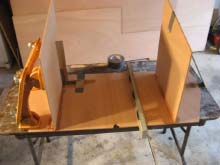 |
Transom |
Although David is a fan of using the belt sander method as shown
in his video, I am trying a method that uses a jig and circular
saw.
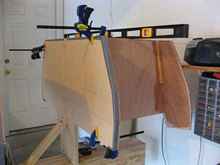 |
Transom mounted |
The jury is still out on the effectiveness of this technique.
I did find out though on the first few tries that my jig guide
strip was too deep, causing the body of the saw to rock on it,
naturally resulting in a wavy cut. Right now the strip is ¾"
deep, so I plan on knocking it down to about 3/8". With the
problem identified, I look forward to making the necessary adjustments
on my jig this weekend, and taking another shot at this splicing
stuff. I'll let you know how things turn out.
David Nichol's Lutra Laker plans are at Duckworks.
Click
Here.
*****
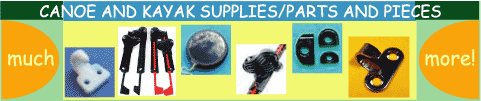
|